I have been using a double bass endpin called RobPin since June of this year.
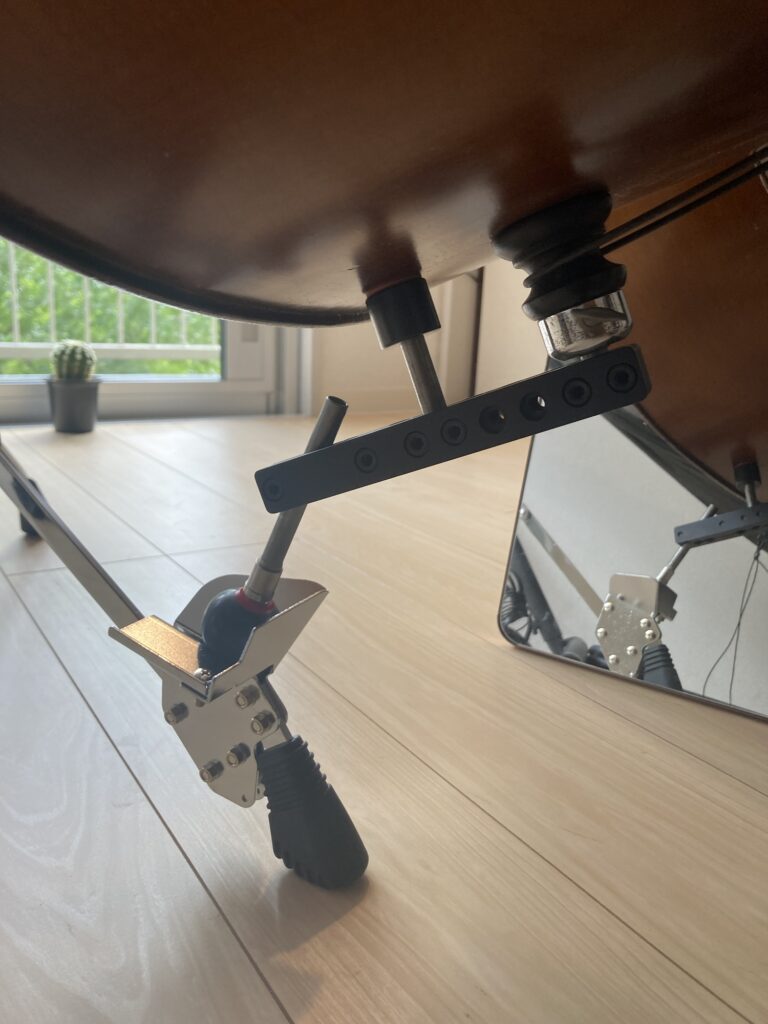
This endpin differs from the typical straight endpin; the endpin is bent, and the center of gravity is slightly behind the double bass endpin socket, near the back. I first became interested in this endpin when I watched on YouTube that Francois Rabbath had drilled a hole in the back of a double bass endpin and added a new endpin.
He talks about being able to use the weight of the arm. He also mentioned that the arco can use the weight of the bow itself, allowing the player to incorporate fewer muscles (around 21:22 in the video). I saw a story on Talkbass.com that jazz bassist John Clayton was also inspired by Francois and drilled holes in Ray Brown’s double bass.
Since direct drilling isn’t practical for most players, I researched alternative options(I looked up “double bass bent endpin” and “angled endpin”) and discovered RobPin. Through some TalkBass threads, I learned that Rob Anzellotti, the creator of RobPin, engages actively with user feedback, providing reliable insights into the endpin’s design. This direct involvement gave me confidence in the product(See also).
I decided to buy it, but was hesitant at first because of the price: Robpin’s price was just under 40,000 yen at the time. But I reasoned that, as a lasting investment, it was worth it to explore the difference an angled endpin could make.
——
Ordering a RobPin isn’t done through a standard website. Instead, I contacted Mr. Anzellotti directly via email. He replied promptly, first asking me two questions:
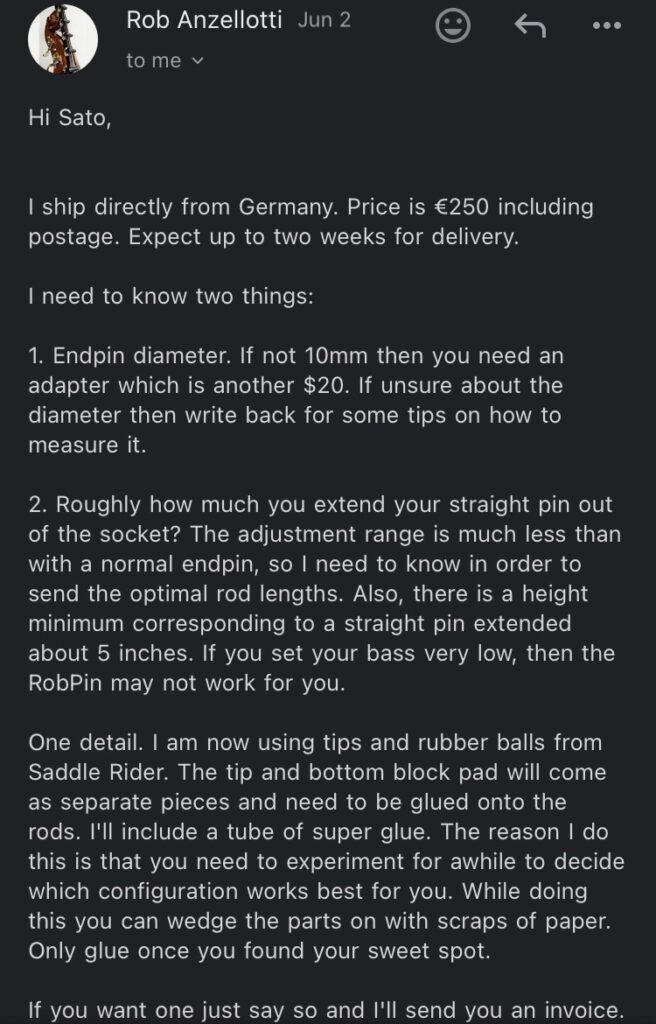
First, the diameter of the endpin is 10mm or not. Second, how long is the end pin I am using extended from the socket? They say they can accommodate a minimum of 5 inches = 12.7cm. I was concerned because my endpin setting was 10 cm, but I told Rob that I had extended it roughly 5 inches (as described later, there was no need to worry).
Mr. Anzellotti then sent me an invoice. Payment was made by foreign currency transfer to the German bank indicated on the invoice. (Payment can be made by foreign currency remittance or Paypal.) When I told him that I had made the payment, he confirmed my current address, so I told him that too, and he shipped the endpin.
It took about a week and a half from shipping to arrival in Japan. The box contained an Allen key for adjustment, four silver rods of different sizes, a black rectangular metal part to insert the rods, and glue (not pictured below). The glue is supposed to be poured into the rod and ball end to fix them in place once you have decided on the setting you like. I didn’t use it because I tucked scotch tape into the ball end part.
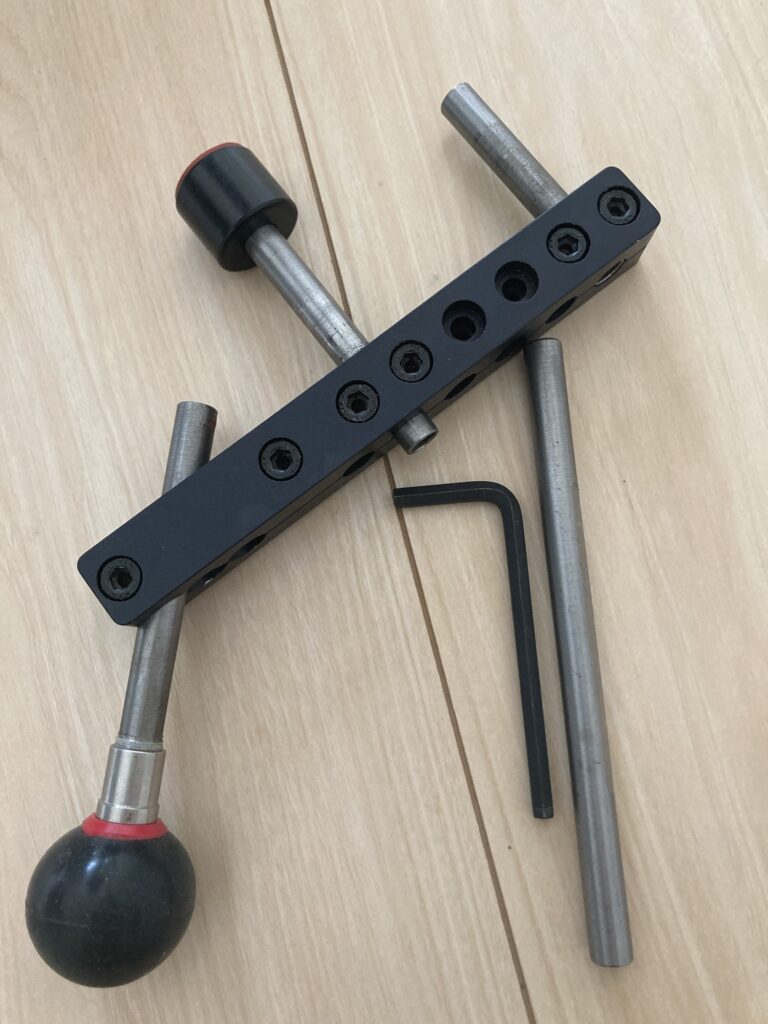
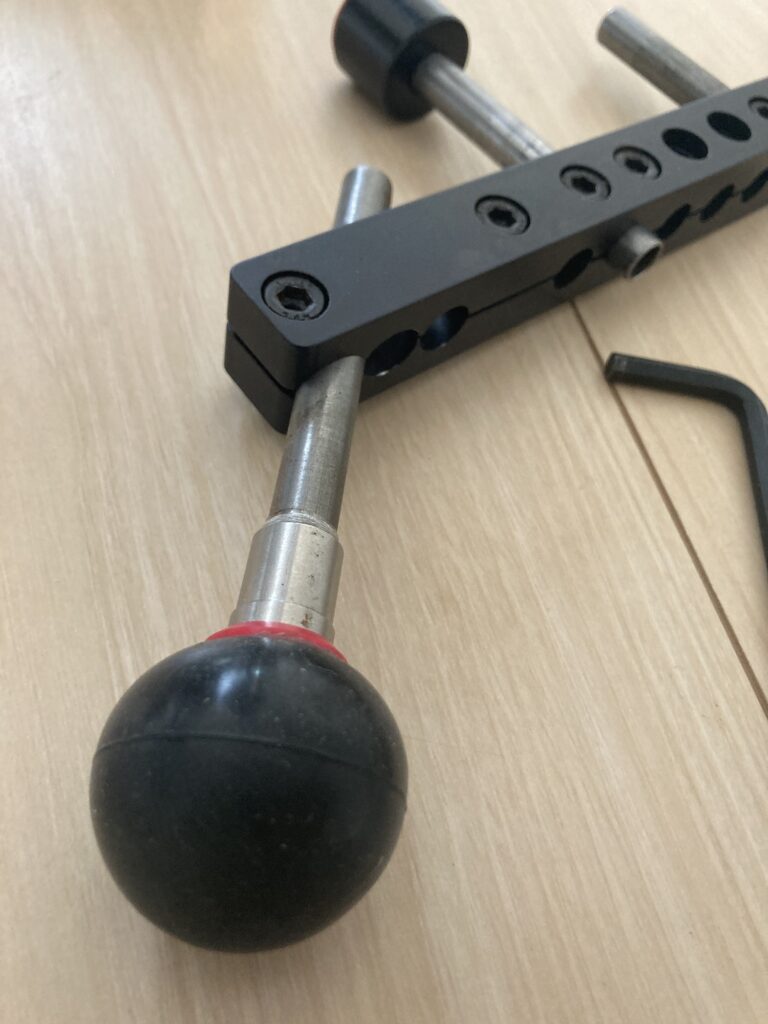
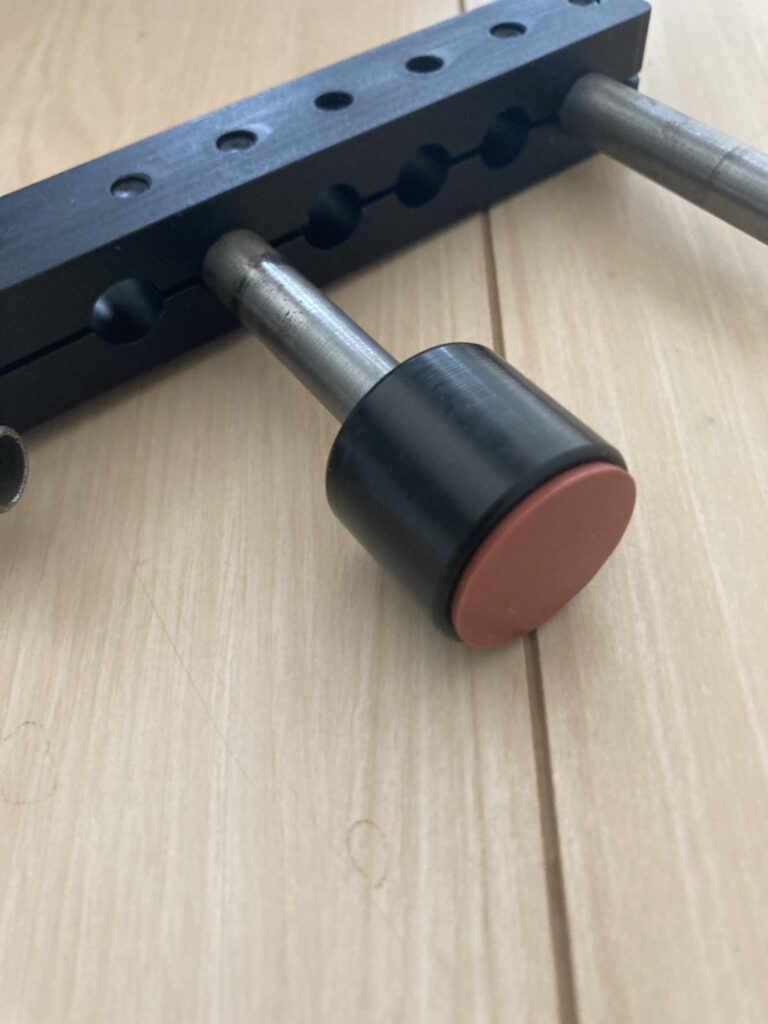
The first thing I felt when I installed it was that the sound of the double bass was louder than before.
I was surprised because I had not imagined that changing the endpin would have an acoustic effect. There are two possible reasons. First, Rob’s silver rods are made from cold rolled carbon steel, which may have a greater acoustic effect than the more commonly used steel. He mentions on Talkbass.com that could-rolled carbon steel was ‘arguably’ superior to stainless steel. See also
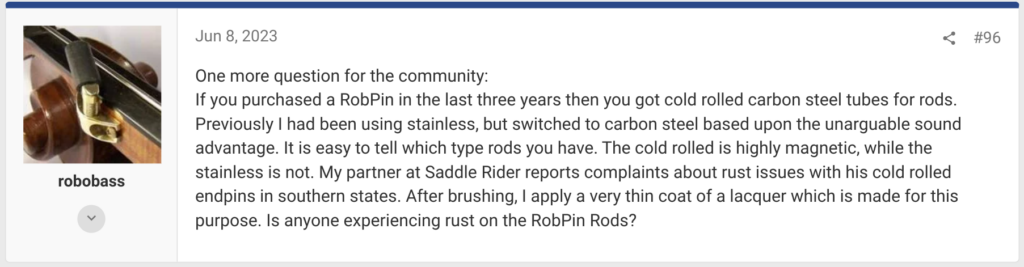
The second reason could be that the curved endpin shape tilts the sound hole slightly upward, making it easier to hear the sound.
My body could not get used to it for about the first few minutes of use. I felt uncomfortable because the fingerboard was not vertical but slanted. However, when my body got used to it after a few minutes, I noticed that access to the thumb position was smooth. In addition, the physical burden of pressing both low and high positions was reduced.
In addition, the Robpin can be moved from side to side with the socket to adjust the posture depending on how the double bass is positioned. For example, virtuoso Lynn Seaton’s double bass is equipped with a bent endpin, not a Robpin, and he has the endpin bent toward the G string.
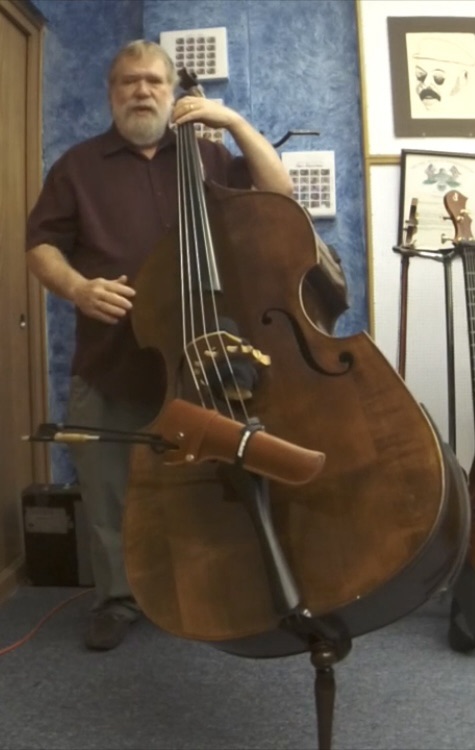
On the other hand, many of the Robpin users on Talkbass.com thought that the Robpin should be tilted toward the E string to stabilize the posture. I started out leaning toward the E string like the Talkbassists, but now I’m leaning slightly toward the G string. The reason for this is that by leaning slightly toward the G string, I wanted to make the fretboard angle more parallel to the ground than at an angle. This may have a negligible effect when pressing the E string, but I thought it would be easier to press the string with the fingertips while maintaining the curved finger of the left hand. It is quite difficult to explain in writing, so here are some pictures.
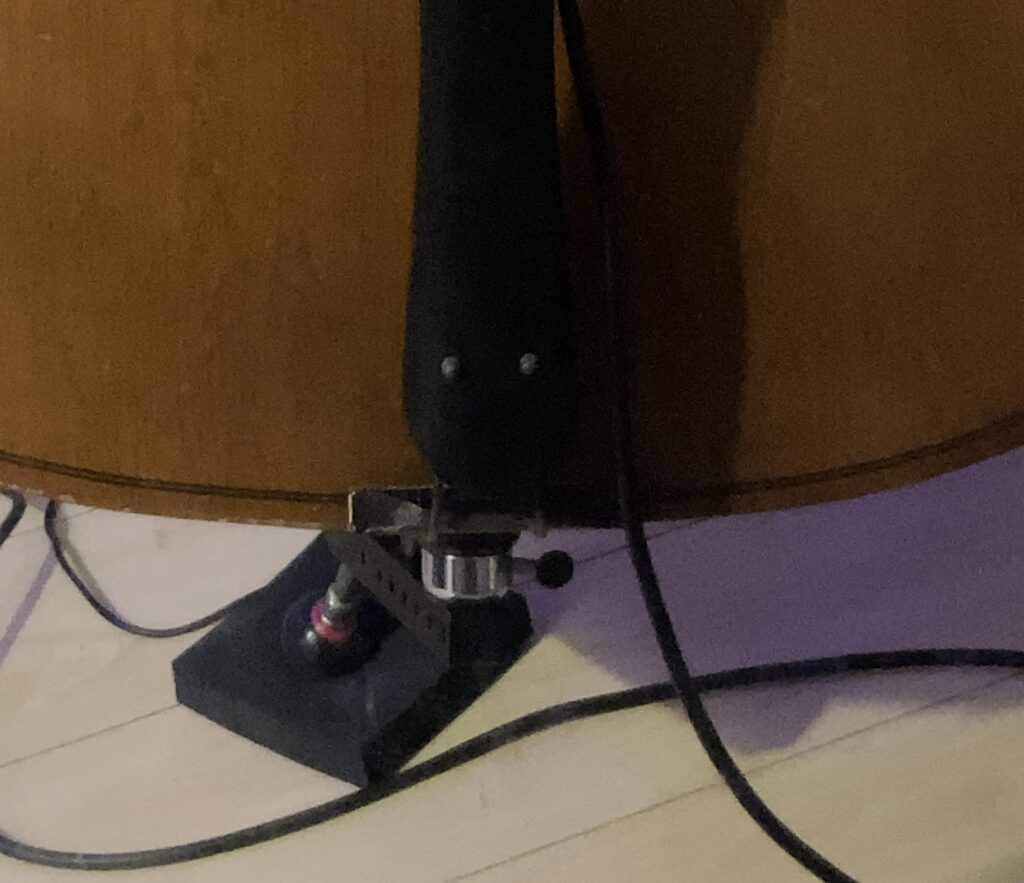
If you are not concerned about the material of cold-rolled carbon steel, you can probably do a DIY by gathering pipe at a home improvement store to make something similar. Also, I had no problem with the 5 inches (12.7cm) limit, as it can be adjusted somewhat lower. The setting can be made lower than the current setup by shortening the bar with the ball end a little more. It can probably be shortened to about 6 cm, so this would be the minimum endpin height that would have to be extended from the socket.
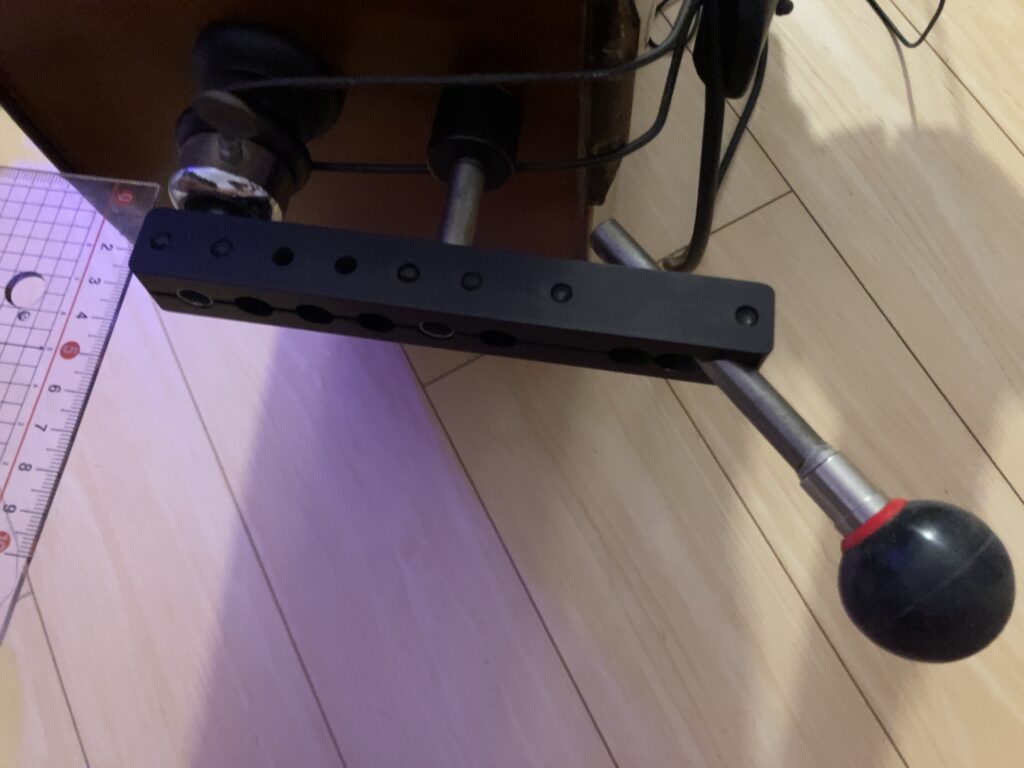
There are some disadvantages as well as advantages. One is that the rubber ball sometimes comes off suddenly, which is not very often as it happens once in a few months. Since it is rotated and attached to the spike part, it becomes loose after use. The other is that the endpin socket part is not completely fixed and the entire Robpin angle shifts. I am not certain however Rob may have recommended using Saddle Rider endpin sockets on talkbass.com. The endpin rotation did not bother me so It’s not a problem for me.
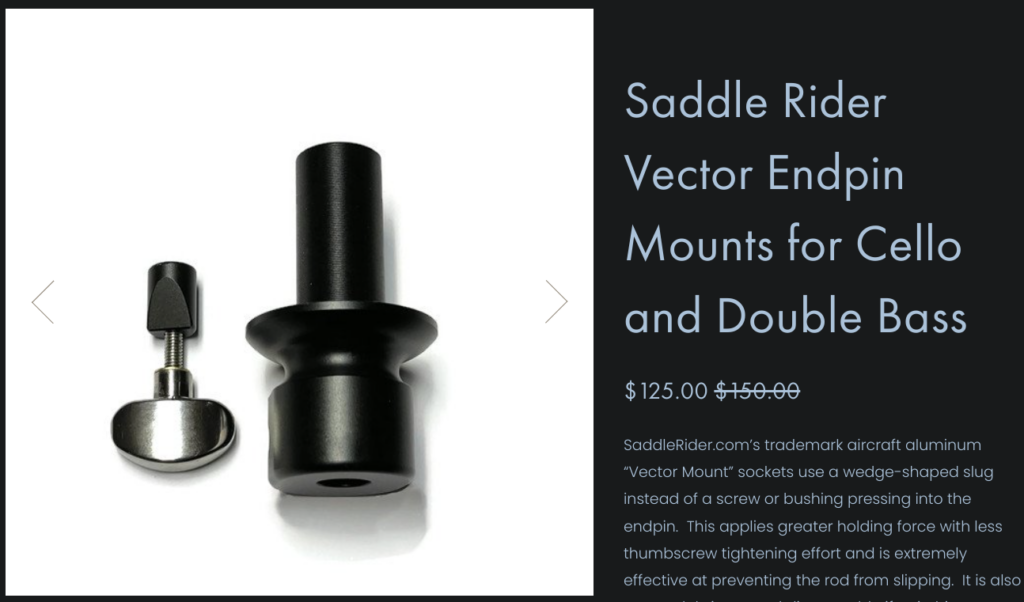
In conclusion, although the high price is a bottleneck, Ropin itself is well made and high quality and it reduces the physical burden on the left hand and makes it easier to access high positions. Shortly, curved endpins like Robin may become more mainstream among bassists than straight endpins.
P.S. (Dec. 18, 2024): Both the slipping rubber ball and accidental rotation of the endpin socket have been resolved, as Rob himself commented on this blog. According to him, the rubber ball has been upgraded to a harder material, providing greater resistance to skating. Additionally, a rod with a flat surface is now included, ensuring the endpin socket stays securely in place without rotating.
Thank you so much BassDog. You have concisely addressed two of the major bugbears with the RobPin. Both have now been solved, well mostly. If you have a traditional 10mm socket, you now get a rod with a flat surface on it which allows the thumb screw to prevent sideways rotation. The rubber balls were indeed slipping off sometimes. I have switched to a slightly harder rubber ball, which will no longer slip off, and will also last longer. It will not resist skating as much as the previous softer rubber, but the geometry of the RobPin much reduces the skating tendency compared to a straight pin.
First of all, thank you, Rob, for creating such an outstanding product. I’ve been using the RobPin with my Yamaha SLB300 electric upright bass, and it’s been a game-changer. The ease it provides, especially when transitioning between the low register and thumb position, has significantly improved my technique. I truly believe this simple yet innovative device has the potential to become a standard for future generations of bassists.
Your clarification about the flat surface rod was really helpful, I hadn’t realized its purpose, but it makes perfect sense now. I’ll be sure to update my blog with this detail. I’ve been using the RobPin with the harder endpin grip that came with the SLB300, and it pairs wonderfully, offering great resistance to skating. So the updated harder rubber ball sounds like a fantastic improvement as well. Thank you again for your thoughtful innovations and for taking the time to share your insights, it means a lot!